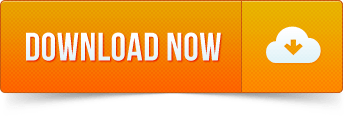
Amercoat 240 quick reference
Components 2 |
Mixing ratio (by volume) | 4 part resin to 1 part cure |
Curing mechanism | Solvent release and chemicalreaction between components |
Volume solids (ISO 3233modified) | 87% ± 3% |
Dry film thickness (per coat) | 4-12 mils (100-300 microns) |
Coats | 1 or 2 |
Theoretical coverage | ft²/gal | m²/L |
per mil (25 microns) | 1395 | 33.5 |
6 mils (150 microns) | 233 | 5.6 |
Mix ratio (by volume): Can be applied as supplied or diluted to a maximum 1:1 by volume with water. Specifications AC-12 conforms to or is listed on the following specifications: AMS 1640 (supersedes MIL-C-38334, Ty I, Cl 1) Note: PPG Aerospace recommends you check the most recent specification QPLs for updated information. PPG 235 - Amercoat Grey Epoxy Primer. Mixing ratio 4:1. Amercoat 450HS is packaged in two components in the proper proportions which must be mixed together before use: 1. Flush equipment with thinner or Amercoat 12 before use. Stir each component thoroughly, then add cure to resin and mix until uniformly blended to a workable consistency. Do not mix more material than will be used within 4 hours at. Amercoat ® products provide the confidence of heavy duty protection against chemical contact, corrosion, abrasion, and impact damage in the harshest of end use environments. Segments demanding heavy protective performance often include Transportation, Oil and Gas, Mining, Agricultural and Construction Equipment, and Industrial Machinery. Revised: February 20, 2020 DURA-PLATE® 235 MULTI-PURPOSE EPOXY P A B67-235 S, C P B B67V235 S H (.
Pot Life, (including induction time) (°F/°C) |
90/32 | 80/27 | 70/21 |
40 min | 60 min | 90 min |
Amercoat 235 Mix Ratio

Thinner | T-10, 65 or 101 |
Equipment cleaner | Thinner or Amercoat 12 |
Drying time @ 6 mils (150 microns) DFT (hours) |
°F/°C | 90/32 | 70/21 | 50/10 | 32/0 | 16/-5 |
dry to touch | 3 | 5 | 10 | 24 | 28 |
dry hard | 6 | 8 | 13 | 30 | 48 |
Cure to Immersion* - Tank Lining Service |
°F/°C | 90/32 | 70/21 | 50/10 | 32/0 | 16/-5 |
(Days) | 2 | 3 | 7 | 7 | 7 |
Recoat/Topcoat time @ 6 mils (150 microns) DFT |
minimum(hours)°F/°C | 90/32 | 70/21 | 50/10 | 32/0 | 16/-5 |
Amercoat 240 | 3 | 5 | 10 | 24 | 28 |
Amercoat 229 Series, 450 Series, PSX 700 | 4 | 8 | 16 | 36 | 48 |
Maximum (months) °F/°C | 90/32 | 70/21 | 50/10 | 32/0 | 16/-5 |
Amercoat 240 | 6 | 6 | 6 | 6 | 6 |
Amercoat 229 Series, 450 Series, PSX 700 | 3 | 3 | 3 | 3 | 3 |
Application Procedure |
1. | Flush all equipment with thinner or Amercoat 12 before use. Stir resin using an explosion-proof power mixer to disperse into a homogeneous mixture. |
2. | Add cure to resin.Mix thoroughly until uniformly blended to aworkable consistency.Induction time 70°F/21°C 15 Minutes |
3. | Do not mix more material than can be used within the expected pot life, 1.5 hours at 70°F.Higher material temperatures will shorten the pot life considerably. |
4. | For optimum application,material should be between 50° to 90°F (10° to 32°C). |
5. | Use only T-10 thinner at 10% by volume,maximum. |
6. | Below50°F additional thinning may be needed and multiple coats required to achieve specified thickness. |
7. | To minimize orange peel appearance, adjust conventional spray equipment to obtain adequate atomization at lowest air pressure. |
8. | Apply awet coat in even, parallel passes with 50 percent overlap to avoid holidays, bare areas and pinholes. If required, cross spray at right angles. |
9. | When applying directly over inorganic-zincs or zinc-rich primers, amist coat/full coat technique may be required to minimize bubbling. This will depend on the age of the primer, surface roughness and conditions during curing. |
10. | Ventilate confined areas with clean air during application, between coats, and while curing the final coat. Prevent moisture condensation on the surface between coats. |
11. | Repair damaged areas by brush or spray. |
12. | Clean equipment with thinner or Amercoat 12 immediately after use. |

Amercoat 235 Tds

Amercoat 235 quick reference
Components 2 |
Mixing ratio (by volume) | 4 part resin to 1 part cure |
Curing mechanism | Solvent release and chemicalreaction between components |
Volume solids (ASTM D2697 modified) | 68% ± 3% |
Dry film thickness (per coat) | 4-8 mils (100-200 microns) |
Coats | 1 or 2 |
Theoretical coverage | ft²/gal | m²/L |
1 mil (25 microns) | 1091 | 26.8 |
5 mils (125 microns) | 218 | 5.4 |
Pot Life, 70° | 4.5 hours |
Environmental Conditions |
Air and Surface Temperature | 20° to 122°F (-7° to 50°C) |
Surface temperatures must be at least 5°F (3°C) above dew point to prevent condensation. At freezing temperatures, surface must be free of ice. |
Drying time °F/°C | 90/32 | 70/21 | 50/10 | 32/0 | 20/-7 |
dry through(hours) | 5 | 10 | 22 | 45 | 62 |
Thinner | T-10, 65 or 101 |
Equipment cleaner | Thinner or Amercoat 12 |
Amercoat 235 Technical Data
Recoat/Topcoat time(@ 5 mils DFT) °F/°C |
Minimum (hours) | 90/32 | 70/21 | 50/10 | 32/0 | 20/-7 |
Amercoat 235 | 2 | 4 | 8 | 16 | 28 |
Amercoat 229 Series | 3 | 4 | 7 | 12 | 40 |


maximum (days) °F/°C | 120/49 | 90/32 | 70/21 | 50/10 | 32/0 | 20/-7 |
Amercoat 235 | 30 | 30 | 30 | 30 | 30 | 30 |
Amercoat 229 Series | 1 | 4 | 5 | 5 | 7 | 7 |
Amercoat 450 Series | 1 | 4 | 5 | 5 | 7 | 7 |
Cure to immersion | 7 days |
Ppg Amercoat 235 Pds
Application Procedure |
1. | Flush all equipment with thinner or Amercoat 12 before use. |
2. | Stir base using an explosion-proof power mixer to disperse pigments. |
3. | Add cure to resin. Mix thoroughly until uniformly blended to a workable consistency. Induction time 70°F/21°C 15 minutes |
4. | Do not mix more material than can be used within the expected pot life, 41.2 hours at 70° F. |
5. | For optimum application, material should be from 50° to 90° F (10° to 32° C). |
6. | Use only PPG recommended thinners at 1 pint/gal. Below 50°F additional thinning may be needed and multiple coats required to achieve specified thickness. |
7. | To minimize orange peel appearance, adjust conventional spray equipment to obtain adequate atomization at lowest air pressure. |
8. | Apply a wet coat in even, parallel passes with 50 percent overlap to avoid holidays, bare areas and pinholes. If required, cross spray at right angles. |
9. | When applying directly over inorganic zincs or zinc-rich primers, a mist coat/full coat technique may be required to minimize bubbling. This will depend on the age of the Dimetcote, surface roughness and conditions duringcuring. |
10. | Ventilate confined areas with clean air between coats and while curing the final coat. Prevent moisture condensation on the surface between coats. |
11. | Repair damaged areas by brush or spray. |
12. | Clean equipment with thinner or Amercoat 12 immediatelyafter use. |
Note: Consult Code of Federal Regulations Title 29, Labor, parts 1910 and1915 concerning occupational safety and health standards and regulations, as well as any other applicable federal, state and local regulations on safe practices in coating operations |